Maintenance Technician
Franklin, WI

Job Summary
Purpose
The Maintenance Technician is responsible for performing routine maintenance, troubleshooting, and repairing of equipment, machinery, and facilities to ensure safe and efficient operations. The role involves carrying out preventive and corrective maintenance tasks, diagnosing mechanical and electrical issues, and ensuring a high standard of quality and safety.
Responsibilities
- Perform routine inspections and maintenance tasks on equipment, machinery, and facilities.
- Follow preventive maintenance schedules to ensure equipment operates efficiently and to reduce downtime.
- Lubricate, clean, and adjust equipment as necessary.
- Diagnose mechanical, electrical, and plumbing issues with equipment and machinery.
- Perform repairs, replacements, and adjustments to faulty systems or components.
- Use tools and diagnostic equipment to identify the cause of malfunctions and repair or replace parts as needed.
- Assist with the installation and setup of new equipment or machinery.
- Calibrate machines and equipment to ensure accurate and effective operation.
- Test and verify system functionality after repairs or installations.
- Ensure all maintenance work is performed in compliance with health, safety, and environmental regulations.
- Follow safety procedures and use personal protective equipment (PPE) when working with machinery or hazardous materials.
- Report unsafe conditions or potential hazards to management.
- Maintain accurate records of maintenance activities, repairs, and inspections.
- Document inventory usage and order replacement parts or supplies as needed.
- Report any major issues, repairs, or equipment malfunctions to the Maintenance Manager.
- Collaborate with the Maintenance Manager and other team members to address issues and improve system reliability.
- Support production teams by ensuring equipment downtime is minimized and that systems are running smoothly.
- Provide input into ongoing maintenance projects or facility improvements.
- Monitor and maintain an inventory of parts, tools, and supplies used for maintenance activities.
- Order materials or parts as needed to complete repairs or preventive tasks.
- Suggest improvements to processes, equipment, or maintenance schedules to enhance operational efficiency.
- Stay up-to-date with new tools, techniques, and technologies in maintenance practices.
Skills
- Knowledge of mechanical, electrical, and plumbing systems.
- Experience with automation troubleshooting and repair.
- Experience with tools, machinery, and diagnostic equipment used in maintenance.
- Strong problem-solving skills and attention to detail.
- Ability to work independently and as part of a team.
- Good communication and organizational skills.
- Willingness to work flexible hours, including weekends or evenings if needed.
- Proficiency in computer systems and maintenance management software (e.g., Limble).
Qualifications/Requirements
- Certification in relevant technical field preferred (e.g., HVAC, electrical, industrial maintenance).
- Minimum of 5 years proven experience in maintenance or a related technical field.
- Experience in FDA-regulated medical device manufacturing and/or cleanroom environments is preferred.
- Clearance of favorable background investigation required.
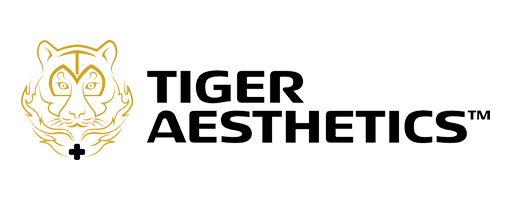
- Franklin, WI
- Operations-TAM
- Full Time
- Senior Maintenance Technician
Tiger BioSciences and its subsidiaries are proud to be an equal opportunity workplace. All qualified applicants are considered for employment without regard to race, color, religion, age, sex, sexual orientation, gender identity, national origin, disability, military or veteran status, genetic information, or any other characteristic protected by applicable law.